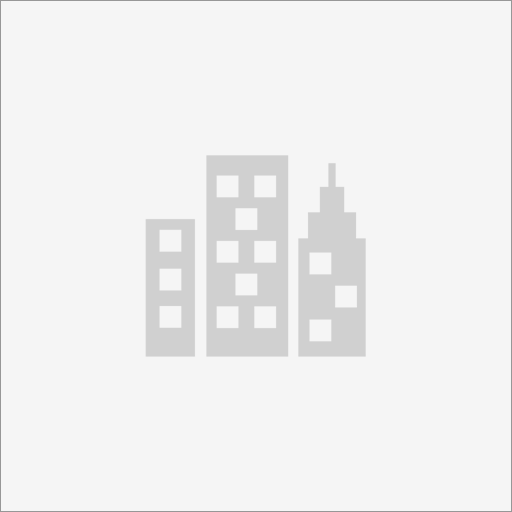
bayt.com
Job Description
Job Description and Qualifications
COMPANY PROFILE
Air Products Qudra is a regional development and investment joint venture (JV) between Air Products and Qudra Energy, a subsidiary of Vision Invest. Air Products is a world-leading industrial gases company developing, engineering, building, owning and operating many of the world’s largest industrial gas projects. Vision Invest is a leading development and investment Holding Company in the Kingdom of Saudi Arabia, with a diversified portfolio of investments across several sectors such as Utility, Infrastructure, Logistics and Industrial Gases with a global operational investment footprint.
NATURE & SCOPE
The Maintenance Manager, reporting to the Operation and Maintenance Director, is responsible for the management and execution function, managing a multi skilled internal and contractor team, in the planning, coordinating, and organizing of activities for preventative and corrective maintenance, with the aim of reducing maintenance related costs while improving plant reliability and availability, in line with business needs for the Jubail Industrial Gas Hub Complex located in Jubail, Saudi Arabia. The Complex includes a Steam Methane reformer which produces Hydrogen and Steam, a CO2 recovery and compression system, and an Air Separation plant which includes storage and delivery, in addition to al the ancillary systems required to operate the untis. The position is responsible for implementing cost effective common systems cascaded by the Reliability and Maintenance Solutions Team to ensure consistent application of Air Products global engineering standards, maintenance best practices, maintenance training, computerized maintenance management systems, and work processes. The position is responsible for managing to a maintenance budget, as developed with the Operations and Technical Teams, which aligns with the Business needs.
PRINCIPAL ACCOUNTABILITIES
Safety
- Provide & maintain a safe work environment. Demonstrate leadership with all company & industry safe work processes to prevent all injuries.
Technical
- Provide technical direction for maintenance related activities for troubleshooting, maintenance, repair, and test activities.
- Provide Maintenance support & guidance during the commissioning of the plants. Maintain accurate document control and monitor quality assurance initiatives in order to maintain the history going forward.
- Provide Maintenance leadership to insure safety, reliability and maintainability of the equipment, instrumentation and electrical processes.
- Provide Maintenance input for scheduled outages to insure contractual requirements are achieved.
- Identify cost savings opportunities in spare parts by leveraging engineering skills and experience to repair
- Assist in the development and manage the preventative / predictive maintenance system to insure scheduled maintenance activities are completed and remain in compliance
- In cooperation with Engineering manege a reliability program to achieve operational excellence by sustaining equipment operation and drive productivity to increase efficiency
Maintenance
- Insure the safety of all maintenance personnel by utilizing the APQ Basic Safety Practice program, which includes Safety Work Permits, LOTO, Confined Space, etc. The position is a key member in building the Air Products safety culture into the APQ
- Understand Environmental Regulatory requirements
- The Maintenance Manager must foster a climate where the focus of the work force is centered on safety, quality and team growth
- Establish the maintenance organization and support construction and commissioning activities
- Manage the Maintenance team consisting of a contract coordinator, planner, mechanical, electrical, and instrument technicians, & warehouse management by balancing the internal & contractor workforce, based on data driven decisions to insure safety and reliability targets are met to achieve maximum profitable
- Build the plant maintenance’s team capability through support coordination from Air Product’s Global teams and in Kingdom subject matter experts.
- Provide coaching and motivation to the maintenance team to achieve operational excellence and customer satisfaction
- Insure APQ & Air Products standards, and best practices for EH&S, productivity, reliability, quality, and overall customer services are met
- Working with the operations and engineering teams understand plant issues and provide cost effective solutions for resolution to meet the customer’s satisfaction on safety, reliability, product quality, and flexibility on product supply
- Facilitate attainment of operations excellence and customer satisfaction via maintenance productivity, reliability, quality, cost reduction, services, and meeting of budgets.
- Provide maintenance support and participate incident investigations and Root Cause Analysis. Identify & implement sustainable corrective action(s).
- Provide leadership in turnaround (TAR) planning and execution, including maintenance and repair information collection, preparation of job packages, spares and materials, contractors and tools, safety management during execution, and TAR execution and contractor management
- Act as the Single Point of Contact for the Maintenance Department when dealing with internal issues of the onsite units ( ASU, HYCO, CO2, etc), representing APQ and coordinating internal resources. Provide timely progress updates to the stakeholders.
- Emergency response required 7 days a week/ 24 hours a day. The Maintenance Manager must have the ability to make decisions upon consulting operations and engineering outside of normal working hours on the resolution of the issue at hand
Skills
MINIMUM REQUIREMENTS AND QUALIFICATIONS
- A minimum of a Bachelor degree in an engineering field (Mechanical, Chemical, Electrical, or Instrument & Controls)
- 10 years minimum in gas, petrochemical, or related industries in operations, construction, engineering, and/or maintenance function. Air Separation and or HYCO Operations a plus.
- 8+ years in maintenance supervision with a demonstrated understanding of the maintenance work process with a track record
- Demonstrated technical and practical engineering skills with a good business sense in the maintenance field
- Proven coordination experience in a multi team environment which includes engineering and maintenance.
- Good leadership, interpersonal and teamwork skills with the ability to communicate clearly and effectively throughout all levels within the organization and externally.
- Promotes a ‘one team’ environment
- Strong oral and written skills with the ability to communicate and manage maintenance activities to the complexes management team on a daily basis.
- Proven problem solving skills
- Knowledge of the construction and maintenance of large and complex rotating equipment (e.g. compressors, turbines, pumps, expanders), pressurized systems, control and instrumentation, and electrical equipment and systems
- Proficiency in English speaking and writing.
- Knowledge and understanding of local environmental and health and safety requirements.
- Strong computer skills, knowledgeable in maintenance software programs, with a background in SAP a plus
- Demonstrated leadership and decision making skills are critical to the position.